Walk Behind Compactor PME-C330
When you are looking for a plate compactor, we can assist you in selecting the most suitable walk behind compactor for your business.
Walk Behind Compactor PME-C330
The PME-C330 Walk Behind Compactor is a heavy-duty machine designed for large-scale compaction projects. Powered by the highly reliable Honda GX390 engine, this compactor is built for maximum performance and durability, making it ideal for professional contractors working on demanding jobs.
Unmatched Compaction Power
With an impressive plate size of 83 cm x 68 cm, the PME-C330 delivers a powerful centrifugal force of 38 KN, allowing it to reach a maximum compaction depth of 90 cm. Operating at a frequency of 3,750 VPM, this compactor ensures deep, uniform compaction, making it perfect for large projects such as road construction, foundations, and landscaping. Its travel speed of 25 meters per minute and efficiency of 850 square meters per hour ensure high productivity and fast completion of even the most challenging jobs.
Ideal for a Wide Range of Applications
The PME-C330 is designed to handle a variety of soil types, including both cohesive and granular materials. Its large plate and high compaction force make it suitable for heavy-duty applications such as compacting asphalt, gravel, or soil in preparation for roadways, parking lots, and large construction sites. Its ability to operate on sloped surfaces with a maximum inclination angle of 20° adds to its versatility.
Built to Endure Heavy Use
Constructed from premium materials, the PME-C330 is engineered to withstand the harsh conditions of intense use. Weighing 270 kg (net) and 255 kg (gross), this machine is solid and dependable. Packaged in a convenient size of 91 cm x 51 cm x 114 cm, it is designed for easy transport and storage. The PME-C330 also comes with a 1-year product warranty, ensuring that professionals can rely on it for long-term, effective performance in the most demanding environments.
Applications
- Retaining Walls
- Footings and Foundation Projects
- Landscapes and hardscapes
- Patchwork on Asphalt
- Pipeline Applications
- Road Repair and Trenchwork
- Cohesive Soils and Granular Soils
- Sticky soils – such as clay or clayey silt
- Gravel, sand, silt, clay, or mixed soils
- Base, Subbase, Subgrade, Subsoil
- Backfill Pools, Parks, Cemeteries, and Golf Courses
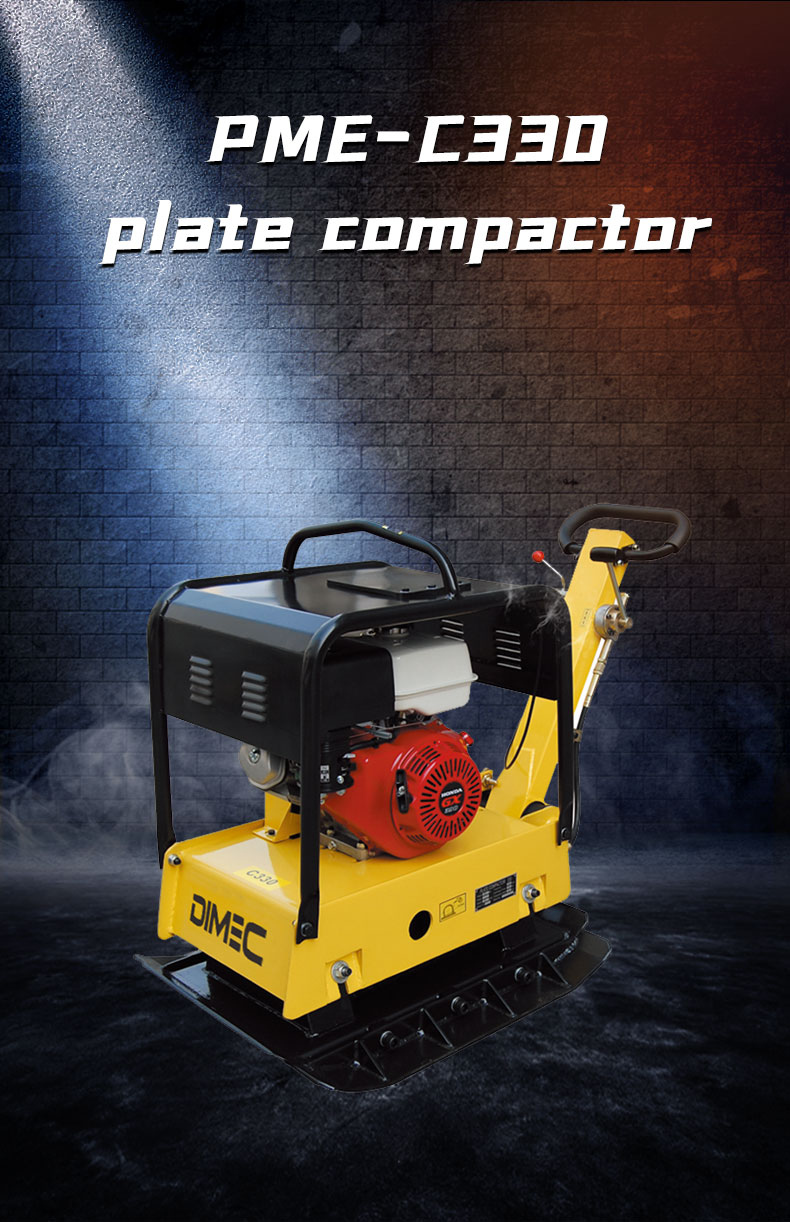
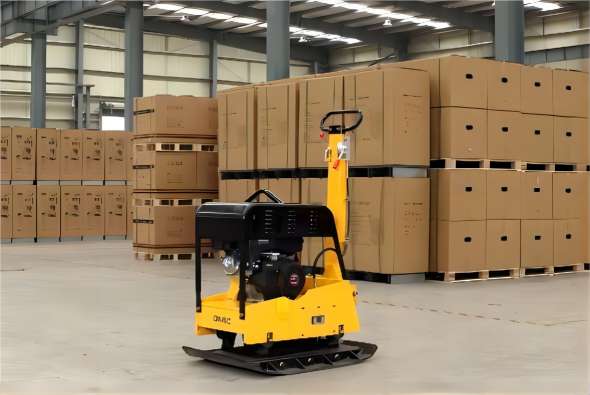
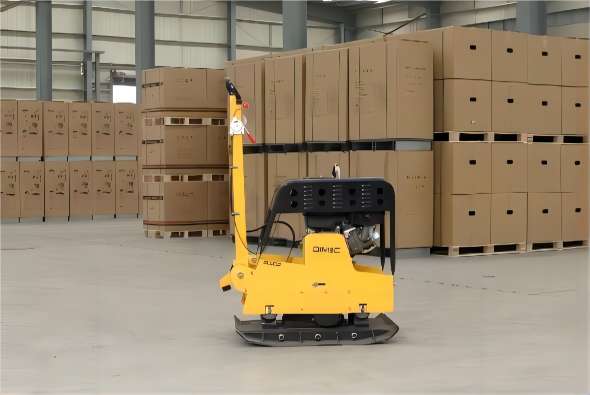
Key Specifications
Model | Walk Behind Compactor PME-C330 |
---|---|
Engine | Honda / Robin / Loncin / Diesel engine |
Engine type | Air-cooled, single cylinder, 4-stroke, petrol engine / diesel engine |
Frequency [VPM] | 3750 |
Centrifugal force [KN] | 38 |
Plate size (LxW) [cm] | 83x68 |
Max.compaction depth[cm] | 90 |
Travel speed [m/min] | 25 |
Max.inclination angle | 20° |
N.W./G.W. [kg] | 255/270 |
Package (LxWxH) [cm] | 91x51x114 |
ADVANTAGE

Low vibration comfortable operation
Heavy-duty shock absorber system that effectively improves operating comfort by reducing shock to arms.
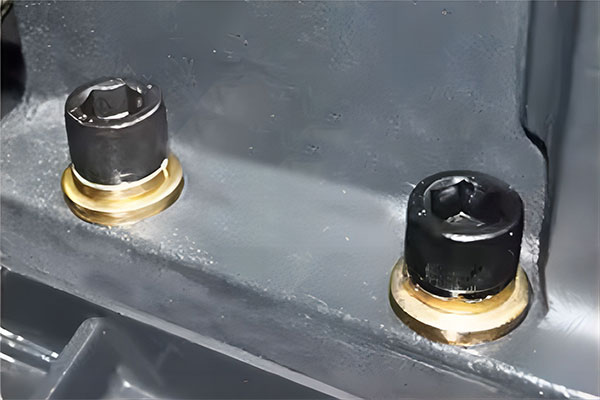
12.9 Grade bolts
High-strength bolts with exceptional durability, providing reliable fastening even under intense pressure and demanding conditions.

High strength engine frame
The material of thickened steel pipe has strong supporting force and stable gravity bearing capacity.

Strong power brand engine
Well-know brand engines Honda, Robin, Loncin low noise, low maintenance, low consumption.
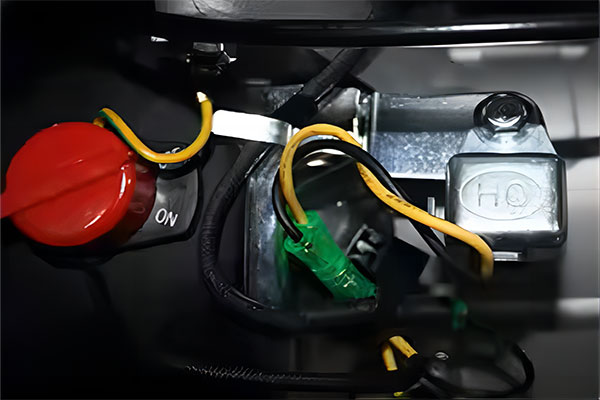
Low oil sensor
Advanced low oil sensor technology ensures automatic engine protection by preventing operation when oil levels are insufficient, extending engine life.
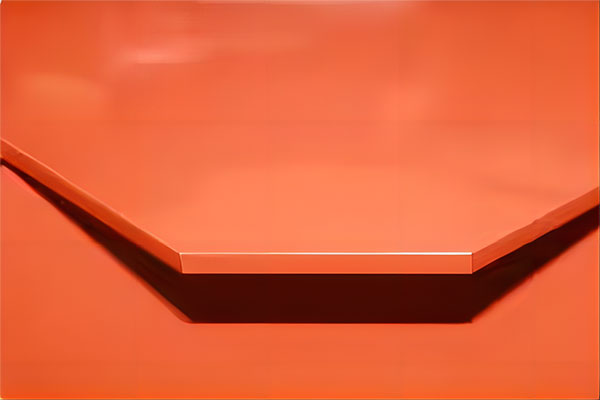
Professional spraying process
Utilizes advanced spraying techniques to deliver a smooth, even coating that resists wear, corrosion, and fading, ensuring long-lasting protection and aesthetic appeal.
QUESTIONS & ANSWERS
Overcompacting can lead to surface damage, making it difficult for water to drain, which may result in cracks or erosion over time.
No, different soil types require different compaction techniques. For example, sand and gravel work best with vibratory compactors, while clay might need additional water and pressure.
Regular maintenance, including oil changes, air filter cleaning, and drive belt inspections, should be performed after every significant project or according to the manufacturer’s recommendations.
Personal protective equipment such as gloves, safety boots, and ear protection should always be worn when operating a walk-behind compactor.
Running a test pass and checking the soil’s resistance and appearance can help you determine if further compaction is needed.
Other Similar Products
20+ Years of Experience
Construction Machine Manufacturer
Professional manufacturer of small construction machinery, main products include plate compactor, tamping rammer, road roller,floor saw, concrete vibrator, generator etc.
Reversible Plate Compactor
A reversible plate compactor is a type of construction equipment specifically designed to compact and stabilize soil, gravel, sand, asphalt, and other granular materials. Unlike standard, forward-moving compactors, reversible plate compactors can move both forward and backward, allowing for greater maneuverability and efficiency, especially in confined or tight spaces.
Reversible plate compactors are essential tools for construction professionals who require efficient, versatile, and powerful compaction solutions. They enhance productivity, improve compaction quality, and provide greater control and ease of use in a wide range of applications.
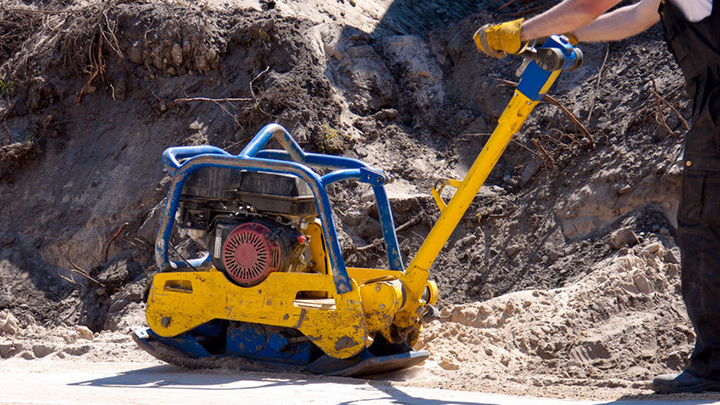
8 Common Mistakes When Using a Walk Behind Compactor
Introduction
Using a walk-behind compactor might seem straightforward, but there’s more to it than meets the eye. Whether you’re a DIY enthusiast working on your backyard or a professional tackling larger projects, compaction plays a crucial role in achieving solid, long-lasting surfaces. However, making mistakes when using a compactor can lead to uneven surfaces, structural issues, and even damage to your machine. Avoiding these common errors can save you time, money, and effort in the long run.
Let’s explore eight common mistakes people make when using a walk-behind compactor and how you can avoid them for smoother and safer operations.
H1: Failing to Understand the Type of Soil
Soil is not a one-size-fits-all deal. Different types of soil react differently to compaction, which means using the same approach for all soil types can backfire.
H2: Different Soil Types and Compaction Needs
Gravel, sand, clay, and silt—each of these soil types requires different handling. For instance, granular soils like sand and gravel compact easily with vibration, while cohesive soils such as clay might need more pressure or water to reach proper compaction.
H3: Why Soil Understanding Matters
If you don’t take the time to analyze the soil you’re working with, you could end up with a poorly compacted surface. For instance, compacting wet clay too quickly can result in soft spots, while over-vibrating granular soils could lead to segregation, which is just as bad.
H1: Overcompacting the Surface
You might think the more you compact, the better, right? Not always. Overcompaction can lead to unintended consequences.
H2: How Overcompacting Leads to Surface Damage
When you overcompact a surface, you can actually break down the soil particles, causing the surface to become too dense. This can make it hard for water to drain, leading to issues like erosion or cracking in the future.
H3: Optimal Levels of Compaction
The key to avoiding overcompaction is to know when to stop. Usually, a few passes are all you need, depending on the type of soil and the compactor. Pay attention to the feel of the machine and the surface—it’ll tell you when it’s enough.
H1: Using the Wrong Compactor for the Job
Walk-behind compactors come in different varieties, each designed for specific tasks. Using the wrong type can lead to inefficient work and potential damage.
H2: Different Types of Walk-Behind Compactors
There are plate compactors, rammer compactors, and vibrating rollers, to name a few. Plate compactors are best for granular soils like sand and gravel, while rammers are ideal for cohesive soils like clay.
H3: Matching Compactor Type to the Job
Make sure you select the right machine based on your soil type and project needs. For example, using a rammer on granular soil might lead to uneven compaction, while a plate compactor on clay may not provide enough pressure.
H1: Neglecting Regular Maintenance
Your walk-behind compactor is like any other machine—it requires regular maintenance to function properly. Skipping this step can lead to breakdowns at the worst possible moment.
H2: Importance of Maintenance for Machine Longevity
Neglecting maintenance shortens the lifespan of your compactor. Dirt, grime, and wear can build up, leading to mechanical issues and inefficiency.
H3: Key Maintenance Tasks for Walk-Behind Compactors
Regular oil changes, cleaning the air filter, and inspecting the drive belts are all essential. Additionally, always check the plate for signs of wear and tear, as a worn plate can reduce compaction effectiveness.
H1: Ignoring Manufacturer Guidelines
Every walk-behind compactor comes with specific guidelines from the manufacturer, and ignoring them can cost you more than you realize.
H2: Why Following Guidelines Increases Efficiency
Manufacturers include these guidelines for a reason—following them helps you use the machine as efficiently as possible. From the type of fuel to use to recommended operating speeds, these details matter.
H3: Avoiding Costly Repairs with Proper Usage
Ignoring guidelines might result in costly repairs or replacements. Something as simple as using the wrong type of fuel or not allowing the machine to cool down can lead to serious damage.
H1: Operating on Uneven Surfaces
Your walk-behind compactor is built for flat, even surfaces. Using it on uneven ground can result in poor compaction and even injury.
H2: Why Flat Surfaces are Crucial
Flat surfaces ensure that the compactor distributes its weight evenly, leading to uniform compaction. On uneven surfaces, the machine can wobble, which affects its performance.
H3: The Risks of Uneven Compaction
Uneven compaction can lead to weak spots in your surface, which may cause cracking or sinking over time. Always prep your site to ensure it’s as flat as possible before you start compacting.
H1: Inadequate Safety Measures
Safety is paramount when operating heavy machinery like a walk-behind compactor. Unfortunately, many people overlook basic safety precautions.
H2: Personal Protective Equipment (PPE)
Always wear the necessary PPE, such as safety boots, gloves, and ear protection. These machines are loud, and without ear protection, prolonged exposure could lead to hearing damage.
H3: Safe Operating Practices
Make sure to operate the compactor with both hands on the controls and avoid wearing loose clothing that could get caught in the machine. Also, keep a safe distance from other people while working.
H1: Not Monitoring Water Levels (for Wet Soils)
For soils like clay, water plays a significant role in achieving optimal compaction. Not monitoring water levels can result in subpar results.
H2: Role of Water in Compaction
Water acts as a lubricant for soil particles, allowing them to settle into place more easily. But too much or too little water can ruin the compaction process.
H3: Balancing Water for Optimal Results
It’s important to monitor the moisture content of your soil. If the soil is too dry, it will be difficult to compact; if it’s too wet, it can become unstable.
H1: Skipping Test Runs
A test run helps ensure that your compactor is working effectively and that the soil is reacting as expected.
H2: Importance of Running Test Passes
By doing a test pass, you can gauge how the soil is compacting and make necessary adjustments before committing to the entire area.
H3: Adjusting Based on Test Run Feedback
Test runs allow you to fine-tune the compaction process. Whether it’s adjusting the water content or the number of passes, a test run ensures everything is on track before the final compaction.
Conclusion
Using a walk-behind compactor correctly is essential to achieving a stable and long-lasting surface. By understanding the type of soil you’re working with, choosing the right compactor, and following proper operating and maintenance practices, you can avoid common mistakes and get the job done efficiently. A little extra attention to detail can make all the difference in the quality of your work.
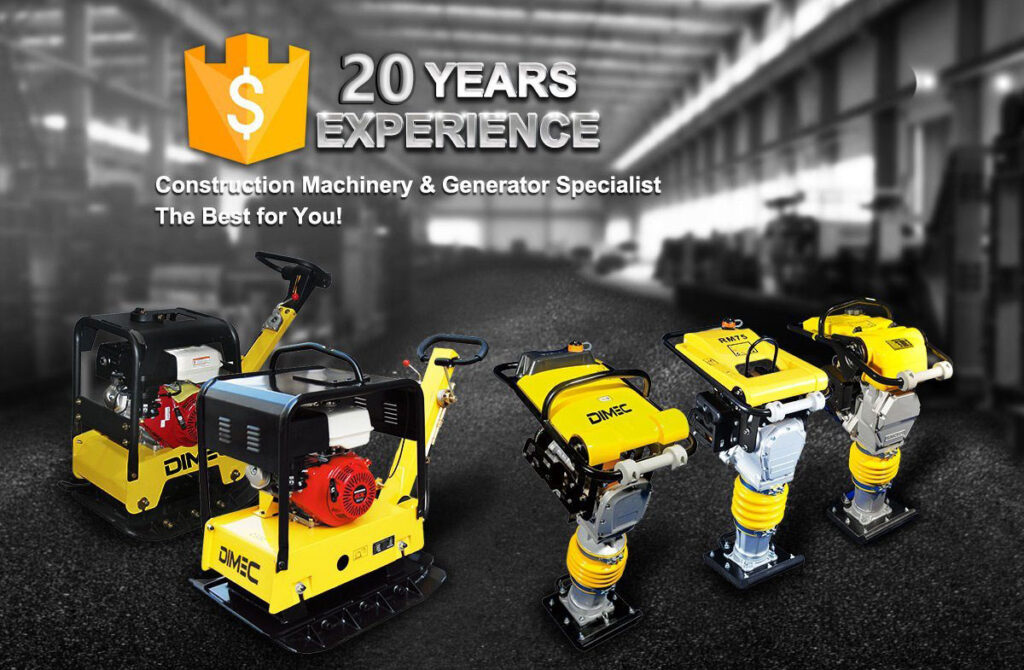
About Us
Wuxi Pinnacle Mechanical Equipment Co., Ltd. (PME) As a first-class specialty enterprise we serve global clients. PME specialize on production of plate compactor, tamping rammer, floor saw, concrete vibrator for global construction industry. We also produce engine, generator, and water pump. PME’s strengths are rooted from our strong team and rich resources.
We have complete production and assembly lines for different machines. There is a team of chief engineers, senior technicians and QC inspectors, equipped with a variety of finishing, spare parts inspection and product testing equipment, to safeguard production and innovation. Thus, we can control every step of production, from finish machining of spare parts, steel plate cutting and welding, spraying paint, all the way to product assembly. This results in effective product quality control.
With more than 20 years of exporting experience, PME has been exporting to over 68 countries and regions including North America, South America, Europe, Southeast Asia, Middle East, Africa. We also form strategic corporations with many multinational companies.
Factory Show
Let our expertise in custom Forward Plate Compactor take your projects to the next level.
Why Choose Us
Professional construction machinery manufacturer with OEM service
We are a leading manufacturer in the construction machinery industry, offering top-notch Original Equipment Manufacturer (OEM) services. Our commitment to innovation and precision engineering ensures that our machinery meets the specific needs of our clients, providing customized solutions that enhance efficiency and performance on the job site.
20 years production and exportation experience
With two decades of experience in production and exportation, we have built a strong reputation for delivering reliable and high-quality construction equipment worldwide. Our extensive knowledge and expertise in the industry enable us to understand the unique challenges of different markets, ensuring our products are tailored to meet global standards.
20+ types of construction site equipment are available for selection
We offer a diverse range of over 20 types of construction site equipment, catering to various industry needs. From heavy-duty machinery to specialized tools, our product lineup is designed to support every phase of construction, providing our clients with the flexibility to choose the right equipment for their projects.
10+ years QC monitor products quality
Our rigorous quality control processes have been refined over more than 10 years, ensuring that every piece of equipment we produce meets the highest standards. Our dedicated QC team meticulously monitors every stage of production, guaranteeing that our products deliver consistent performance and durability in the field.
8+ years experienced skilled workers
Our team comprises highly skilled workers with over 8 years of experience in the construction machinery industry. Their expertise and dedication are reflected in the precision and craftsmanship of our products, ensuring that every detail is executed to perfection.
8 workshops, 12 production lines
With 8 state-of-the-art workshops and 12 production lines, our manufacturing capabilities are designed to meet large-scale demands efficiently. Our advanced facilities allow us to maintain a streamlined production process, ensuring timely delivery of high-quality machinery to our clients around the world.
Unlock Superior Construction Efficiency with Our Expertly Engineered Machinery
Discover a world of advanced construction equipment tailored to meet the demands of modern job sites. With 20 years of industry experience and a commitment to quality, our machinery is designed to boost productivity and ensure reliability in every project. Explore our diverse range and experience the difference of precision-engineered solutions.